How does a certified reliability engineer identify failures or risks? They look at the factors that increase a failure rate and help determine whether an issue or component must be repaired replaced, or improved upon. To successfully design a manufacturing process or product, a CRI needs to understand the life cycle, which is a product’s most important life-cycle stage. The CRI then identifies how changes in processes or components impact the end life of the system. This is called the warranty life or the degraded life.
The goal of a certified reliability engineer is to reduce system-wide failure rates. They help to reduce costs by identifying unnecessary parts, testing new designs to improve efficiency, testing equipment and tools for performance, implementing new diagnostic techniques to detect failures early, training employees to properly perform maintenance and repair operations, determining the cause of mechanical failure, and improving the efficiency of non-firewalls and software in the network. The certified reliability engineer also helps to certify that the organization’s processes, products, and/or services meet stated objectives. In addition, they ensure that the organization’s facilities meet building standards.
According to ACI International, “measurable, consistent, reliable, and complete” are the three primary requirements of a system or a product to be certified. Achieving these three goals ensures the reliability and maintainability of a system. In addition to these requirements, an FMEA is required to provide information on a manufacturer’s history, track record of accomplishments, management of manufacturing, quality management systems, workshop practices, FMEA reviews, performance monitoring, FMEA audits, and FMEA compliance. The purpose of these reviews is to monitor and improve manufacturer performance. Reviews are also performed to reduce or eliminate variability and failures.
Certified reliability engineers are required to be licensed by their respective states’ licensing boards. These certifications are achieved through a combination of theory and practical examinations. Applicants can choose to take the Practical Testing portion of the examination. If they choose to take the theory portion, they must first complete a one-hour training session that emphasizes critical analysis topics. Most states require that candidates successfully pass a multiple-choice exam in order to complete their certification.
The most significant advantage of pursuing engineering exams lies in gaining the skills and knowledge required to become a Certified reliability Engineer. Applicants who successfully complete their practical and study examinations are able to fulfill one of two requirement requirements: They are required to be properly trained and certified if they’re eligible to apply for the FMEA, or they have to have enough work experience in the field. Candidates who successfully complete the exam and receive the certification are then qualified to apply for the FMEA. Those who do not pass the practical exam and lack the work experience are not qualified to apply for the FMEA.
The purpose of a Certified reliability engineer is to reduce the manufacturing cost of a product by improving the overall product life cycle. The Certified reliability engineer must first evaluate the entire product life cycle. This includes a determination of the processes that occur throughout the product’s life, as well as data collected during testing and manufacturing. Next, the engineer must determine the cause of failures and problems. If defects are identified and fixed, quality problems will decrease. Individual redesigns to improve upon design deficiencies will also decrease product failure rates.
To become a certified reliability engineer, candidates need to successfully complete at least one of the following courses: Product Life Cycle, Engineering Analytic Design, Qualitative Analysis and Testing, or Product Development. Once qualified, candidates must complete the National Council for Industrial Credit Card (NCIC) Qualification Test or obtain an NCIC credit card. Candidates who successfully complete the requisite number of hours will be given their certificate.
Related Certification Exam:
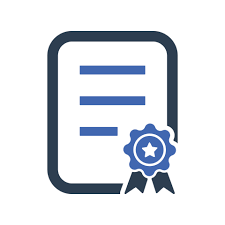
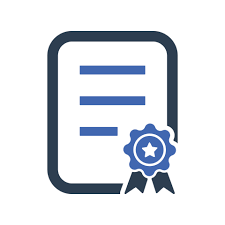
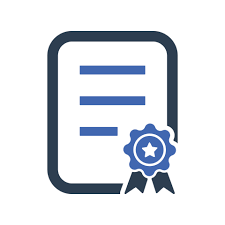
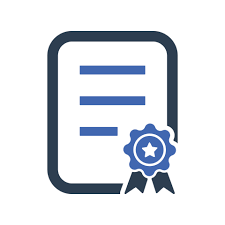
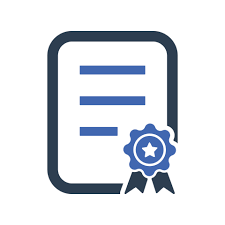
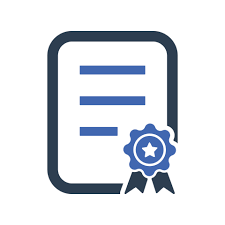
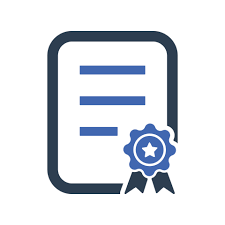
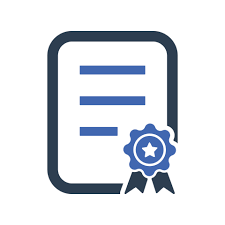
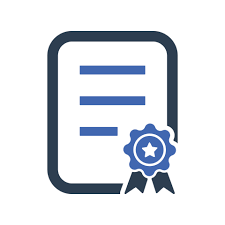
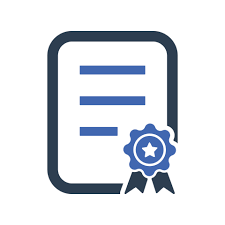